JUNA Technology Announces 3,000+ Hours, 3,000 Starts and Stops of Alkaline Electrode Stability Data
JUNA Technology recently released performance data from industrial-scale electrolyzers, including over 3000 hours of continuous operation at 6000 A/m² and two separate 1000+ hour runs at 10000 A/m². In addition, the company completed a 3000-cycle start-stop durability test with consistent performance throughout.
These combined results mark the first dual-track verification of the JA series alkaline electrodes’ ability to maintain stable operation under high current density while also tolerating frequent system cycling. This milestone offers the green hydrogen industry a highly practical, engineering-ready electrode solution.
Exceptional Long-Term Stability: JUNA’s JA Alkaline Electrode Demonstrates Low Degradation Under High Current Density
As the green hydrogen industry moves toward cost-driven competition and scaled deployment, reducing system costs while maintaining safety and efficiency has become a key concern for alkaline electrolyzer developers. Against this backdrop, increasing current density has emerged as a central engineering strategy. High-current-density operation offers the potential to reduce the number of plates, electrodes, and diaphragms, shrink system footprint, and lower material costs—all while enabling more responsive and modular system designs.
However, operating under high current density also intensifies electrochemical reactions. Electrodes must withstand greater gas bubble impact and current stress, posing significant challenges to long-term durability and performance. Thus, whether an electrode can maintain low degradation, low energy consumption, and reliable safety under high current density has become a defining criterion for engineering feasibility.
To address this, JUNA Technology has conducted multi-scenario validation across different current density levels for its JA series alkaline electrodes.
At 6000 A/m², the JA electrodes completed over 3000 hours of continuous operation in industrial testing.
Throughout the duration, cell voltage remained stable with no observable degradation, and hydrogen content in oxygen stayed below 1%, demonstrating robust long-term performance under high-stress conditions.
This result reinforces the viability of JUNA’s “high current density, low degradation” technical approach and offers the industry an engineering reference for achieving higher performance and lower costs in green hydrogen production systems.
Note: Test data from Pengzhou Green Hydrogen Centre
More importantly, 6000 A/m² is only the beginning. JUNA has also launched long-duration tests at a more extreme current density of 10000 A/m², pushing the boundary of electrode performance:
Electrolyzer 1: 20 Nm³/h capacity, 394 mm diameter, 40 cells, cell voltage of 1.97 V. The system maintained stable operation with no measurable degradation throughout the entire run.
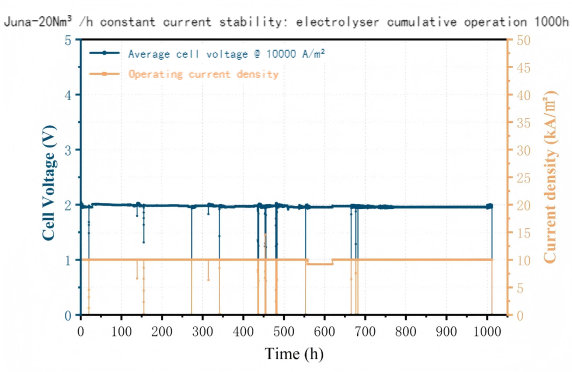
Note: Test data from Pengzhou Green Hydrogen Centre
Electrolyzer 2: 20 Nm³/h capacity, 394 mm diameter, 46 cells, configured with a dimpled plate design. Operating at a cell voltage of 1.87 V, the system achieved a DC energy consumption of 4.47 kWh/Nm³, and showed no voltage degradation after over 1100 hours of continuous testing.
Note: Test data from Pengzhou Green Hydrogen Centre
These findings also highlight the increased demands placed on other system components—such as diaphragms and bipolar plates—when operating at 10000 A/m² over extended periods. Electrolyzer structure optimization is necessary to prevent localized overheating due to delayed gas diffusion and avoid diaphragm burn-through that may result in hydrogen crossover into oxygen streams.
As of now, JUNA recommends 6000 A/m² as the optimal balance point between hydrogen production rate, safety, and energy efficiency. As cylindrical high-pressure alkaline electrolyzer technologies continue to mature, operation at 10000 A/m² or higher is expected to become technically feasible.
This ongoing exploration not only validates the upper performance limits of electrode materials, but also provides a valuable data foundation for future system design and operational strategies under ultra-high current densities.
Second Validation: Electrode Stability Under Start-Stop and Reverse Current Conditions
In renewable-powered green hydrogen systems, load fluctuations and frequent shutdowns often lead to performance degradation in electrolyzers. Among these challenges, reverse current is considered one of the most damaging risks. It typically occurs during system shutdowns when the redox environments of the anode and cathode reverse, leading to loss of active material, catalyst layer collapse, and even complete electrode failure.
Such volatile conditions expose the limits of electrode material durability. To evaluate the performance of JUNA’s electrodes under these stress factors, a series of cyclic forward-reverse current tests were conducted, with traditional Raney nickel electrodes used as a reference.
Key results:
·
Under 1500 A/m² forward current and 150 A/m² reverse current cycling for 500 times, the JA10000 electrode showed only 5 mV voltage fluctuation, compared to 320 mV for the Raney nickel electrode.
·
At 3000 A/m² forward current and 300 A/m² reverse current, JA10000’s voltage fluctuation was 40 mV, while the Raney nickel reached 400 mV, demonstrating over an order of magnitude performance advantage.
This difference stems from the fundamental material and structural design distinctions between the two types of electrodes:
Nanowire Array Structure: Provides large surface area and high transient capacitance, enabling the electrode to absorb reverse current shocks and buffer redox-induced structural changes.
·
NiO/Ni(OH)₂ Composite Protective Layer: Enhances surface electrochemical stability and effectively shields the nickel substrate from reverse current corrosion, preventing structural collapse.
·
Catalyst–Substrate Transition Layer: Forms a strong interfacial bond to prevent catalyst layer delamination.
To further validate start-stop resilience, JUNA conducted a frequent cycling test using a 1212 mm diameter, 30 Nm³/h short-stack electrolyzer. Operating at 3100 A/m² and 85 ± 5°C, the JA series electrode completed over 3000 start-stop cycles.
The test protocol followed the Chinese national standard for electrode performance (effective March 1, 2025). Over a total test duration of 2600 hours, the average cell voltage:
Decreased from ~1.85 V to 1.76 V during the constant current phase
Increased slightly to 1.92 V during the start-stop phase, still well below the 2.0 V threshold for operation resumption.
This testing closely simulates industrial operation under intermittent renewable power conditions, providing robust verification of JUNA electrodes’ real-world stability.
Extrapolating from this data, even with a conservative estimate of 300 start-stop cycles per year, the JA series electrode can support up to 10 years of operation, affirming its adaptability and endurance in renewable-integrated hydrogen systems.
Note: Test data from Pengzhou Green Hydrogen Centre
What Enables a High-Current, High-Stability “Next-Gen” Electrode?
Material selection and process design are the foundational determinants of electrode performance.
When dealing with frequent start-stop cycles and fluctuating loads—common in renewable-powered electrolyzers—the resilience of electrode microstructures becomes the key threshold for large-scale application.
In today’s mainstream alkaline electrode market, common technical paths include:
Thermal-sprayed Raney nickel electrodes
Precious metal-coated sintered electrodes
In-situ growth + electrodeposition techniques (used by JUNA)
Thermal-sprayed Raney nickel, the most widely used method, offers low cost and scalability, making it suitable for mass production. However, in intermittent renewable energy scenarios, these porous structures are vulnerable to reverse current during shutdowns, leading to poor structural stability and rapid degradation. Under high current densities, issues such as catalyst layer detachment caused by intense current and gas flow impact become more prominent.
Precious metal-coated sintered electrodes deliver excellent initial activity, but their strict requirements on operational purity (e.g., low ionic contamination in electrolyte) and high cost limit feasibility for large-scale deployment.
In contrast, JUNA Technology adopts an in-situ growth + electrodeposition approach, enabling precise control over the nanostructure of the catalyst layer. This process yields an ordered nanowire array, which provides:
Superior mechanical stability under high current
Enhanced electron transfer efficiency during electrochemical reactions
Reduced gas bubble adhesion, improving overall performance
The in-situ growth process forms a robust interfacial transition layer between the catalyst and the substrate, preventing catalyst delamination under harsh operational conditions such as high current densities and frequent start-stops. The electrodeposition step ensures uniform distribution of the anode active phase, reducing oxygen evolution overpotential and maintaining stable performance under sustained high loads.
Thanks to this proprietary process, the JA series alkaline hydrogen production electrodes from JUNA Technology have achieved long-term stability and start-stop compatibility under high current densities—offering a technologically viable and engineering-ready solution for the green hydrogen industry.
Multi-Pathway Strategy to Empower the Green Hydrogen Industry
Completing the above performance validations is just the beginning.
Currently, JUNA Technology is advancing toward the next stage of electrode development with a clear focus on higher current density and lower degradation rates, aiming to lay a solid technological foundation for future large-scale, low-cost alkaline green hydrogen systems.
“In response to the rapid growth of the hydrogen industry, JUNA is actively working with leading domestic and international electrolyzer manufacturers to co-develop and validate advanced electrolyzer technologies,”
said a company spokesperson.
“We are targeting breakthroughs in key metrics such as high current density, low energy consumption, wide load adaptability, and start-stop resilience.”
Across alkaline, AEM, and PEM electrode platforms, JUNA has already achieved mass production capabilities and industrial-scale validation, offering a flexible portfolio tailored to varying energy mixes, application needs, and regional strategies. By integrating system-level process R&D with engineering capabilities, JUNA continues to drive cost reduction and performance enhancement across the value chain.
“Several joint projects have now reached the finalization stage. We believe that through close collaboration with industry partners, water electrolysis will achieve deep integration with renewable energy, grid infrastructure, and green chemical production, helping hydrogen play a strategic role in the global energy transition.”
With continuous breakthroughs and extensive field experience, JUNA Technology is building stronger core competencies to support the hydrogen sector as it moves toward a new phase of scale-up and efficiency.